Horst Witte High-Precision Aluminium Machining and Custom Vacuum Fixtures
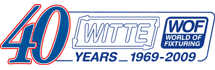
Horst Witte Gerätebau Barskamp, a German based company, specializes in machining high precision products in high-tensile aluminium. This includes design and manufacturing of several innovative, patented fixturing systems for machining and measuring as well as subcontracting machining of top quality parts for aerospace and medical industries.
This company with over thirty years experience in machining aluminium alloys has an ultra modern machine shop and a dedicated workforce with an incredible depth of know-how.
Their subsidiaries in Asia, Mexico and USA as well as additional agents and partners all around the world guarantee qualified advice, supply and service of Witte products.
The Witte company, which is certified according to DIN EN ISO 9001 and DIN EN ISO 9100, has established a quality management system for machining technology for the aerospace industry (such as vacuum and special clamping technology). This quality-management system has been certified to EN 9100:2003, ISO 9001:2000, AS 9100, JISQ 9100 and DIN EN ISO 9001:2000 standards by the TÜV CERT certification body.
The company stands for quality, experience, flexibility and reliability.
AEROSPACE MACHINING AND SUBCONTRACTING
Our aerospace subcontracting activities include machining sheet metal parts for Airbus outer skin. These parts have been milled to required material thicknesses and tight tolerances in specific areas
For machining large, thin sheet metal parts up to 10,000mm x 2,500mm Witte uses their own vacuum clamping systems. This technology allows secure clamping of thin-walled workpieces for milling pockets down to end thicknesses of 0.5mm
Other aerospace subcontracting activities include:
- Machining extruded profiles up to 12,000mm length
- Five axis machining
- Machining brackets out of extruded profiles
- Fixture design, manufacture and assembly using vacuum technology for aerospace companies manufacturing aircraft parts
VACUUM CLAMPING TECHNOLOGY FOR AEROSPACE
Vacuum clamping technology offers individual solutions for safe machining of critical parts, especially if conventional clamping technology does not give acceptable results. Vacuum clamping can be used for nearly every kind of material and machining processes.
Witte offers a large selection of standard equipment and accessories covering numerous applications. For complicated applications Witte designs and manufactures special vacuum solutions, for example for clamping large Airbus components.
CUSTOM BUILT VACUUM FIXTURES FOR AEROSPACE
Custom built vacuum fixtures for aerospace applications have included a 4,500mm long vacuum fixture for friction stir welding of Airbus fuselage. Extendable arms enable mounting of different sized parts, steel inserts cater for heat incurred during friction stir welding process.
VACUUM FIXTURE WITH ROLLER BAR FOR CLAMPING PRE-ROLLED CYLINDRICAL AIRBUS FUSELAGE PARTS
On this custom built vacuum fixture the complete vacuum clamping area measures 4,100mm x 13,000mm. In order to enable manufacture of lightest possible fuselage parts without any loss of quality Witte Bleckede and Airbus Nordenham have developed a special fixture for clamping pre-rolled aluminium sheets during machining.
The total surface of the clamping table is divided in 36 individually operated areas. This means parts of different sizes can be clamped effectively giving a high degree of flexibility. Additional 50 hydraulic and 11 mechanical clamping units ensure part positioning along the sides. This process is an environmental friendly and fast alternative to chemical milling.
VACUUM FIXTURE FOR DEBURRING AIRBUS FUSELAGE PARTS
Fuselage parts for the Airbus-Giant A-380 are mostly made of aluminium and for safety reasons milled out of the solid. Before surface protection, sharp edges have to be removed to ensure sufficient results. This requires not only an appropriate deburring machine but also a suitable workpiece fixture system.
Witte’s solution for this application was a special modular vacuum fixture which comprises of a series of Flip-Pod vacuum chucks mounted on guiderails, enabling secure fixation of different sized parts for deburring. Configuration of chucks and Flip Pods (activated or deactivated according to workpiece contour) is guided via NC controller.
Products and Services
Video
White Papers
Related Projects
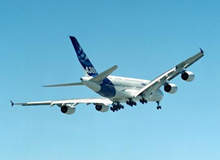
Airbus A380 Superjumbo Airliner
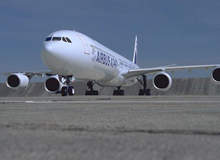
Airbus A340-600
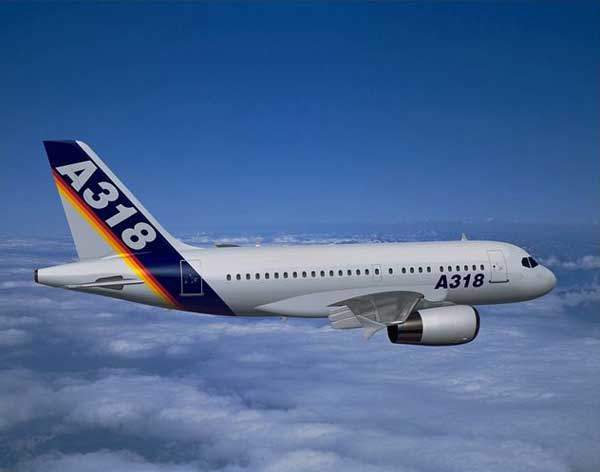
Airbus A318
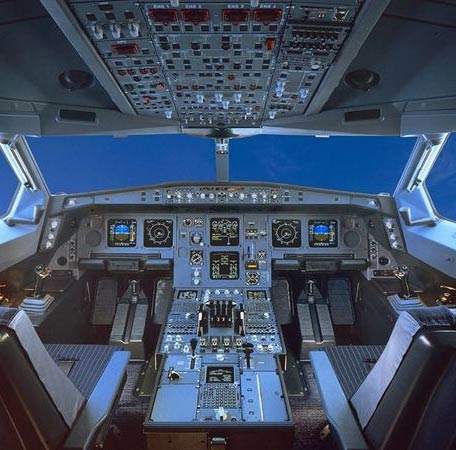
Airbus A340-200 and A340-300
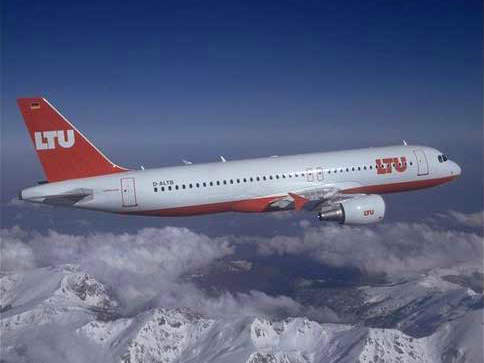
Airbus A320
Press Release
In order to be able to send and receive accurate information from the universe parabolic antennas must be aligned accurately. That means that the base on which the antennas – which weigh several thousand tons – turn must be held in constant position. The core of the Deep Spa
Read moreFor a high-tech company group like AIRBUS production they should be of top standard right the way down the line. Because of this in the Varel plant, where for instance fuselage parts for the AIRBUS are machined, a Fladder machine is being used for deburring of these large alumin
Read moreManufacturing of fuselage parts for different Airbus projects is carried out in Nordenham. Typically in the aircraft industry weight is an important factor and in almost all areas weightsaving has been exploited to the extreme. In order to enable manufacture of lightest
Read moreRegional Offices
Witte Far East Pte. Ltd.
13 Joo Koon Crescent
Singapore 629021
Other
Singapore
Horndorfer Weg 26-28
21354 Bleckede
Other
Germany
Witte America
120 E Market Street Suite 455
Indianapolis, IN 46204
Other
United States of America
Horst Witte de Mexico
Ocotillos No. 3644
31125 Chihuahua
Other
Mexico