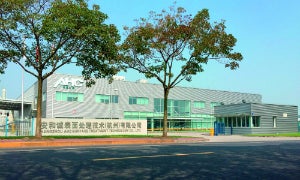
The Dutch industrial company Aalberts Industries has operated a plant for surface treatment of components near Shanghai, China, for about two years, under the name of Hangzhou AHC Surface Treatment Technology Co., Ltd. Since 1 January 2016 this plant has been officially integrated into the AHC Group, which in turn is itself a part of Aalberts Industries NV.
The AHC Group, with its headquarters in Germany, focusses on providing technically functional coatings of surfaces as a service. AHC Hangzhou can draw on over 50 years of coating experience within the AHC Group. The globally active AHC group with more than 900 employees finishes around one billion components annually for many thousands of customers in all key industries. Overall, more than 40 processes and more than 100 process variations are used, and in more than 20 plants for close proximity to customers.
The plant in Hangzhou is very persuasive with its coating quality and its concept of sustainable environmental protection and energy efficiency, which meets the stringent Chinese requirements. Reproducible and robust processes are necessary in order to be able to control the high differentiation of finishing of customer components. For this reason, AHC’s many years of process experience was used in the design of the coating systems and the wastewater technology at AHC Hangzhou. The plant is therefore equipped with the latest technology.
AHC supplies surface coatings for mechanical engineering and for the large system suppliers to the automotive industry, such as Bosch, Schaeffler and TRW Automotive. Fuel pump casings, impellers for turbochargers and control pistons for automatic transmissions, all of them made from aluminium alloys, are protected against wear and corrosion. The large corporations and their system suppliers now have branches in China. For them, AHC in Hangzhou, near Shanghai, is now their local coater.
The 50-member team of AHC Hangzhou provides different processes of anodisation and hard anodisation as well as electroless nickel plating of aluminium components. In addition, non-ferrous metals and ferrous materials, including stainless steels, are also treated with diverse electroless nickel processes. Whereas the first process mentioned produces layers of aluminium oxide, with the second method, the surface is coated with a specific composition of nickel-phosphorus alloy. Hard anodic oxidation of aluminium materials (HART COAT®) and electroless nickel plating of ferrous and non-ferrous materials (DURNI COAT®) are proven surface finishing processes which AHC in Europe has already operated and developed for over 50 years.
In Hangzhou, components up to 1,000kg and dimensions up to 3,000mm (length) x 600mm (width) x 1,200mm (height) are treated in the anodising line. Processes are hard anodising HART-COAT®, HART COAT® GLATT (HC-GL) as well as technical anodising, in each case with the possibility of black colouring and sealing. Components suitable for the electroless nickel plant have a maximum weight of 1,500kg and maximum dimensions of 1,100mm (length) x 600mm (width) x 1,500mm (height). In addition to the DURNI-COAT® process, a variant with incorporated PTFE, the so-called PTFE DURNI-DISP, is also offered. This is a dry lubricant layer having good adhesive wear properties.
The integration of the works in China into the AHC Group is part of the global player’s strategy which AHC is strongly committed to. The implementation of this strategy has been made possible by the strong parent company Aalberts Industries NV, the Netherlands, with 14,500 employees in 200 plants in 30 countries. AHC sees itself on the right path in China and has opened the gateway to the whole of Southeast Asia.