AHC Oberflächentechnik Surface Treatments and Corrosion Protection
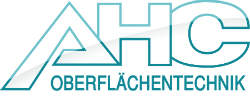
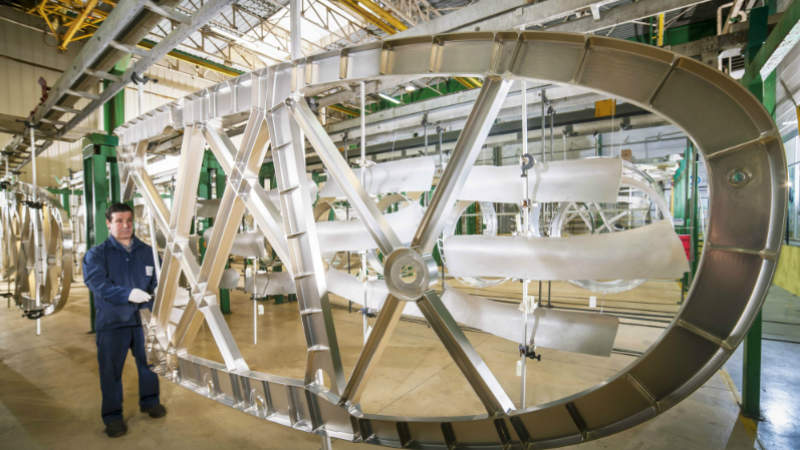
AHC Oberflächentechnik comprises of more than 20 sites with its headquarters in Kerpen, near Cologne, Germany. The core business of the AHC Group is focused on providing functional coating of technical surfaces. The coatings are used in the automotive industry and mechanical engineering market, as well as the aerospace industry and for many other technical sectors where protection against corrosion and wear is essential.
Surface treatments for metal and plastic
The range of services available within the AHC group extends more than 40 processes and many process variants for the surface treatment of metal and plastic, with most being of the processes are patented and proprietary coating processes. We license our patented coatings throughout the world. In addition, we cover the entire requirement of process chemicals globally for processes using chemical and electrochemical treatment of metals and plastics.
Layers for protection against vibration, friction and wear
HART-COAT® layers are formed by anodic oxidation in a cooled acid electrolyte, where the surface of the aluminium base material is converted into an aluminium oxide layer. This layer grows equally inward as outward, creating a specific change in dimension of the component, bonding with the base material. The hardness of the aluminium oxide grants high wear resistance to the layer.
Electroless nickel coatings are layers of nickel-phosphorus alloy, which, through the DURNI-COAT® process, are deposited from aqueous nickel salt solutions, through reduction with hypophosphite, onto the surfaces of ferrous and non-ferrous metals. The process, which runs without external energy, permits uniform layer formation and results in a contour-true reproduction of the surfaces of even those parts with the most geometrically complicated forms.
DURALLOY® is an extremely hard, crack-free, precise, very thin and ultrapure metallic chromium layer. DURALLOY® provides effective protection against friction and vibration corrosion and increases considerably the wear resistance of the material when used, for example, in gears or with shaft-hub-joints.
Depending on the specific requirements these three coating systems are applied on surfaces of valves, nozzles, compressors, screw threads, metal fittings, hydraulic flaps and structural parts subject to vibration.
Plasma-chemical coatings
The plasma-chemical process is used to produce oxide-ceramic layers. In addition to providing a high level of protection against wear and corrosion, also fulfil requirements regarding hardness, uniform layer formation, fatigue strength, dimensional accuracy or temperature load capacity.
MAGOXID-COAT® is suited for magnesium alloys and KEPLA-COAT® is for aluminium and titanium materials. The surface of the layers produced by these processes have a white-grey colour. However, deep-black surfaces can also be created for their optical and thermal properties.
Anti-friction coatings
AHC offers a range of anti-friction coatings, which can be used for door locks, seat bolting devices, slide bearings and bushes, guide mechanisms or seat adjustment components.
Electroless nickel with embedded PTFE particles, called PTFE-DURNI-DISP, is one of the coatings available. The dispersion layer combines the properties of the DURNI-COAT® layer with those of the PTFE. The corrosion resistance and hardness of pure DURNI-COAT® layers are barely affected by the dispersed dry lubricant and the tribological characteristics are considerably improved.
The GLISS-COAT® brand denotes the range of dry lubricant coatings developed by AHC, designed to reduce friction and surface wear. The coating systems and the flow behaviour is modified to avoid any undesirable edge build-up or any drop formation at edges or in bores. Individual parts are coated using automatic flat spray units, while smaller series-produced parts are treated in special barrel-plating devices.
AHC Benelux with its two locations in Eindhoven and Venlo, the Netherlands, have extended the range of services with a number of special anti-friction coatings, named ‘synergetic coatings’. The base layer is either DURNI-COAT® electroless nickel, HART-COAT® hard-anodising or a modified base material. The top layer is always a layer of fluoropolymers. These are made from PTFE, PFA or FEP.
Galvanic coatings
Although not our core business, galvanic coatings such as hard chromium, gold, copper, silver or tin are widely used within the aerospace industry. For instance, silver has the best electrical conductivity of the industrial used metals. This property is useful for electromagnetic shielding. Another example is gold, which AHC uses, with a nickel base layer, for the coating of a space station’s heat exchanger as a shield against radiation.
About AHC Oberflächentechnik
More than five decades after the company was founded, AHC has developed into one of the leading specialists in Europe in the field of surface treatment. With the application-specific and customer-oriented development in our internal R&D departments for surface treatment and chemicals, we wish to help our customers achieve a sustainable success.
In everything we do, people and the environment are close to our heart. Therefore, all our staff take an active role in ecological and social responsibility. We believe in a holistic environmental management system that includes environmentally friendly and resource-efficient processes just as much as harnessing renewable energies.
If you are interested in our range of services, please do not hesitate to contact us.
Products and Services
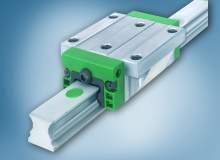
DURALLOY®
DURALLOY® provides effective protection from friction and vibration corrosion via a crack-free, precise, thin and ultrapure metallic chromium layer.
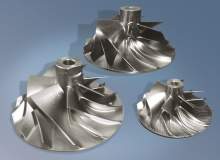
DURNI-COAT®
DURNI-COAT is used to coat ferrous and non-ferrous materials, and is ideal for the coating of metals and plastics.
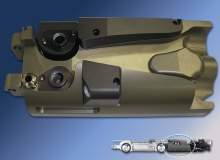
HART-COAT®
Developed especially for the functional improvement of aluminium materials (hard anodising) HART-COAT® is versatile, and can coat almost any aluminium wrought, cast and die-cast alloys.
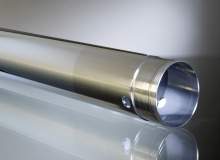
SELGA-COAT® CHROME
SELGA-COAT® CHROME is a hard chrome plating process, which operates with a five-to-six-times-higher current density compared with conventional hard chrome.
Video
Related Projects
Press Release
In 1960, AHC was founded by Ulrich Reininghaus and Herbert Friebe in Mülheim, Cologne, Germany.
Read moreHART-COAT® uses a hard anodising procedure where a protective aluminium oxide coating is electrolytically created on workpiece surfaces.
Read moreThe corrosion and wear protection of seat rails for aircraft made from a high-strength aluminium alloy is improved by a special coating process from AHC Oberflächentechnik.
Read moreAcorn Surface Technology Ltd is a specialist surface treatment company based in Kirkby-in-Ashfield, near Nottingham in the UK, and has been a subsidiary of Aalberts Industries alongside AHC Oberflächentechnik GmbH since 2001.
Read moreThe Dutch industrial company Aalberts Industries has operated a plant for surface treatment of components near Shanghai, China, for about two years, under the name of Hangzhou AHC Surface Treatment Technology Co., Ltd.
Read moreQuality management systems complying with EN / AS 9100ff are becoming more and more important in the aerospace industry. All EN / AS 9100ff certified companies are listed in the OASIS database (Online Aerospace Supplier Information System). This list is now increasingly seen as a prerequisite in order to be admitted as a supplier for the aerospace industry.
Read moreAHC has developed a selective hard chrome plating process, called SELGA-COAT® CHROME.
Read moreA particular coating for aluminium alloys allows the construction of lightweight and easy-to-clean sewer inspection systems.
Read moreLASOX-COAT®: A Novel Method for Selective Oxidation of Aluminium Surfaces Prior to Serial Production
AHC Oberflächentechnik in Germany has developed a novel method for the oxidation of aluminium surfaces.
Read moreRegional Offices
Boelckestraße 25 – 57
D-50171 Kerpen
Germany